As the country increases investment in the environmental protection industry and infrastructure construction, new environmentally friendly materials are increasingly welcomed and accepted by the market. This article briefly summarizes the production equipment, processes, and formulas of the current domestic mainstream PP and PE wood-plastic products for your reference.
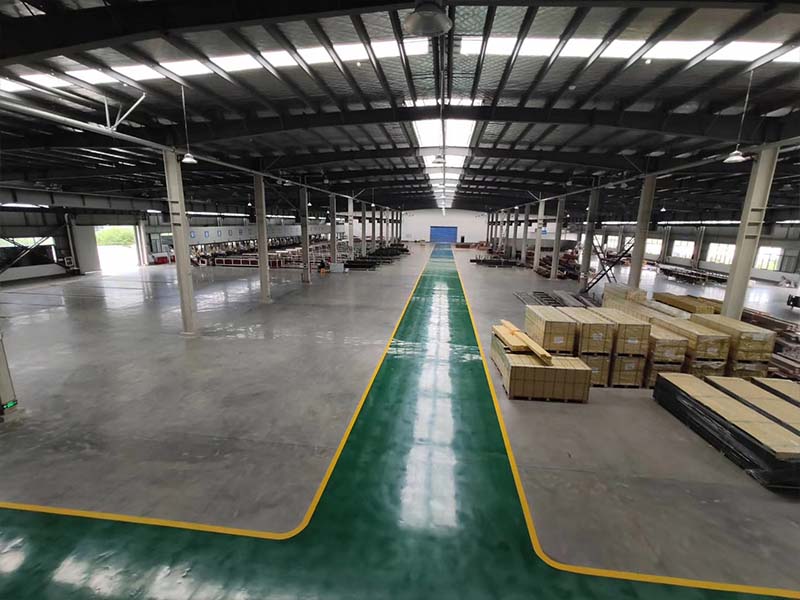

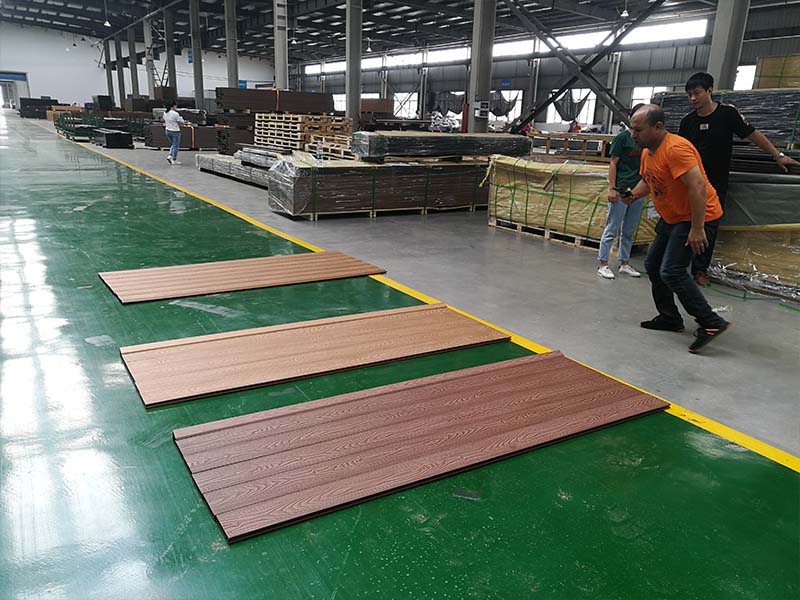
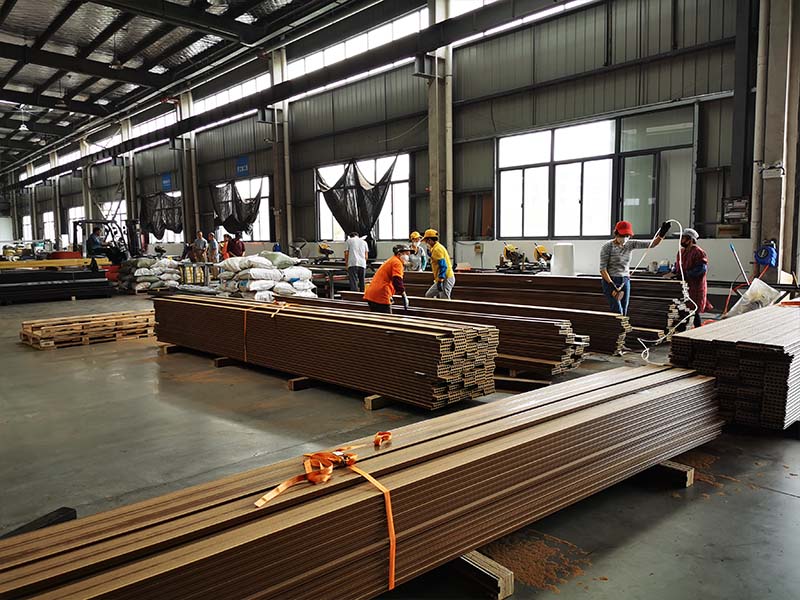
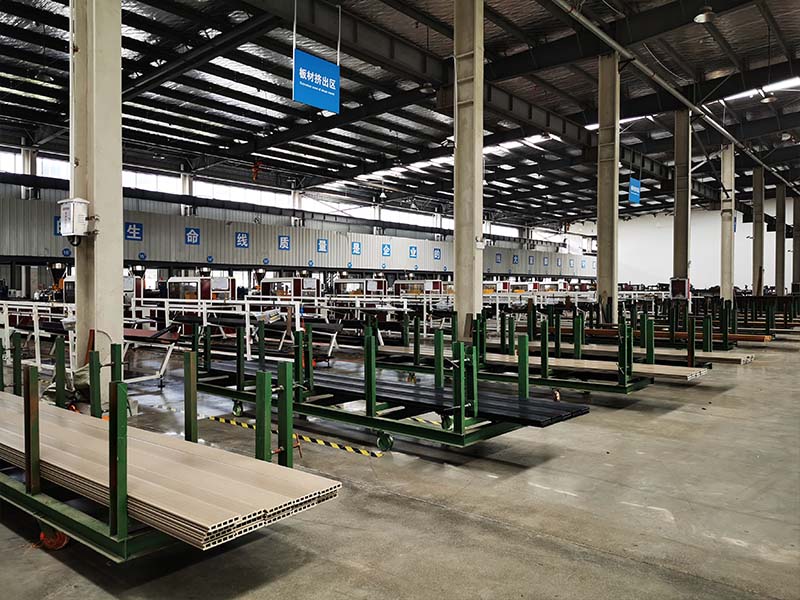
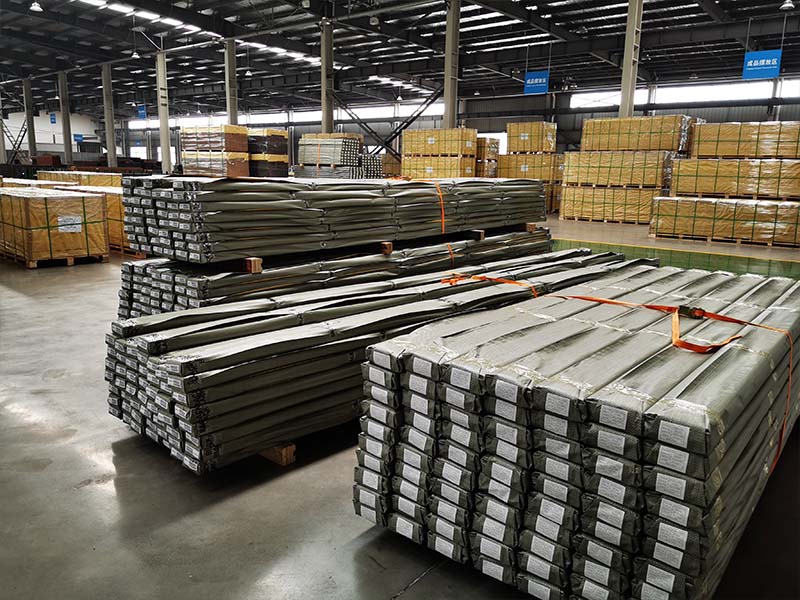
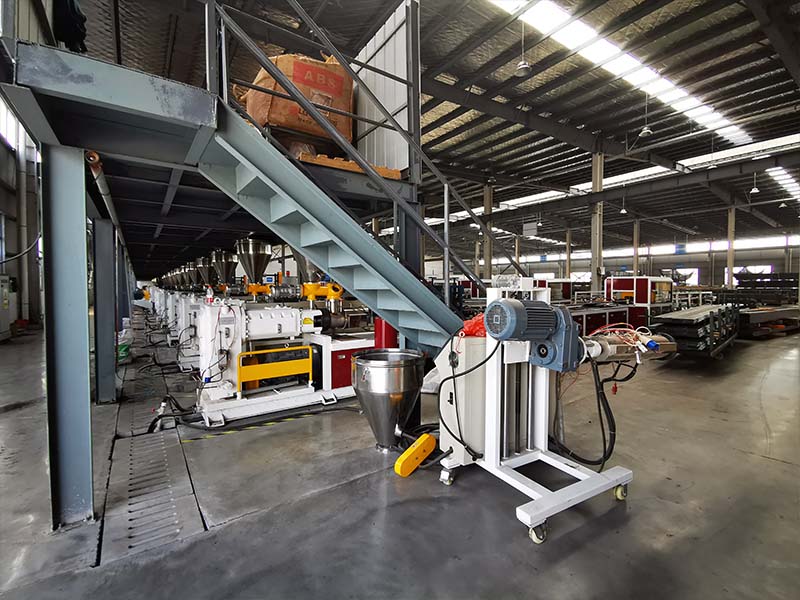
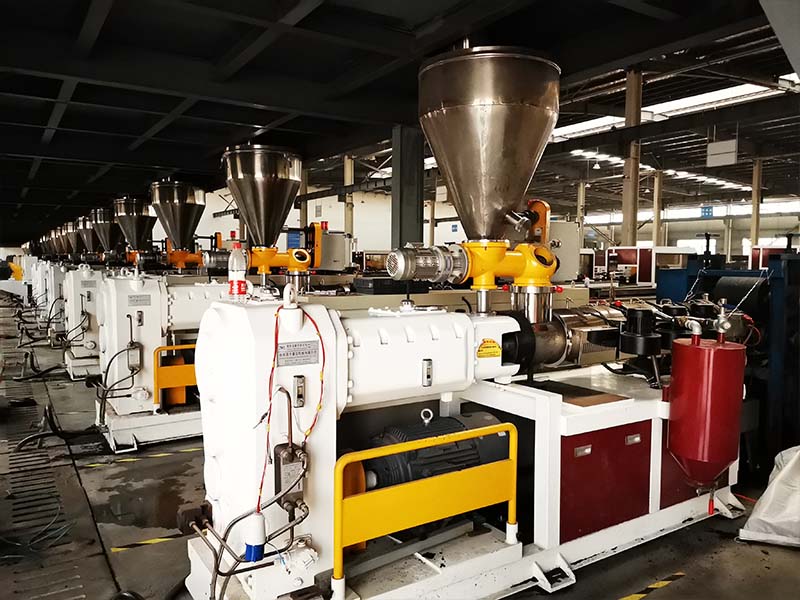
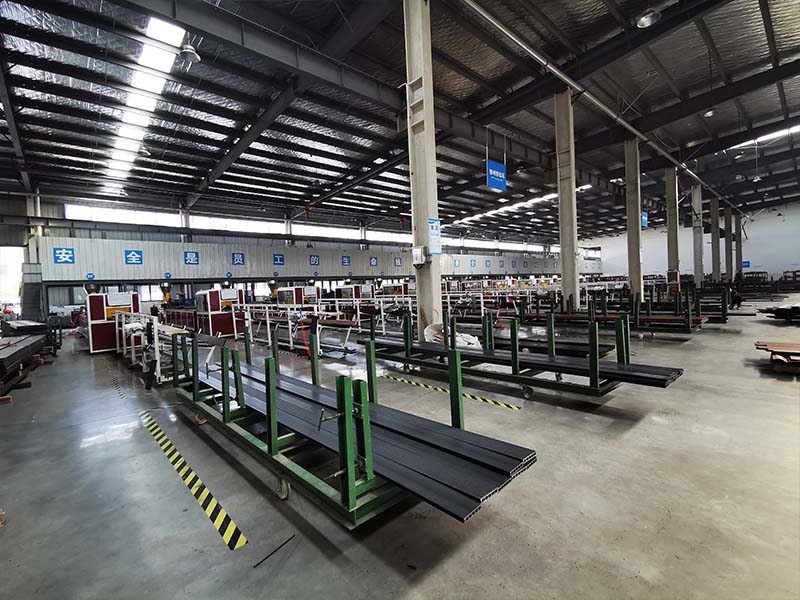
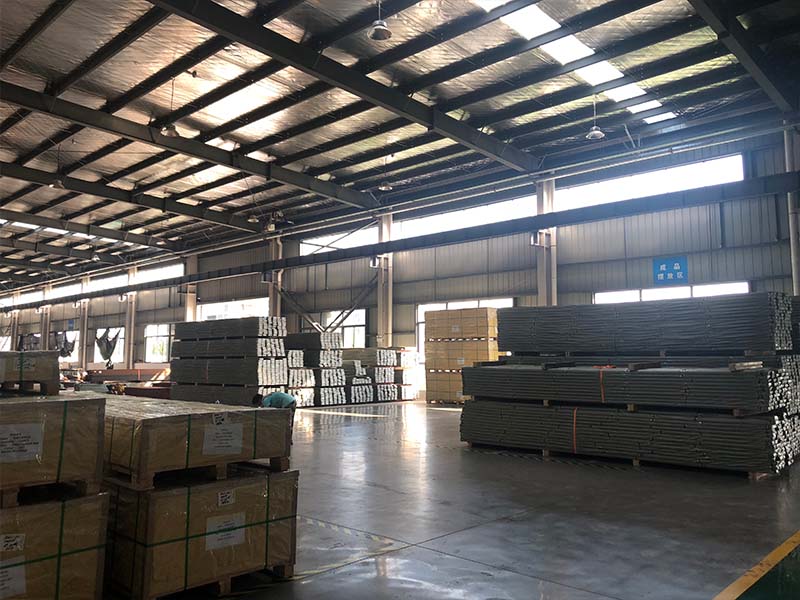
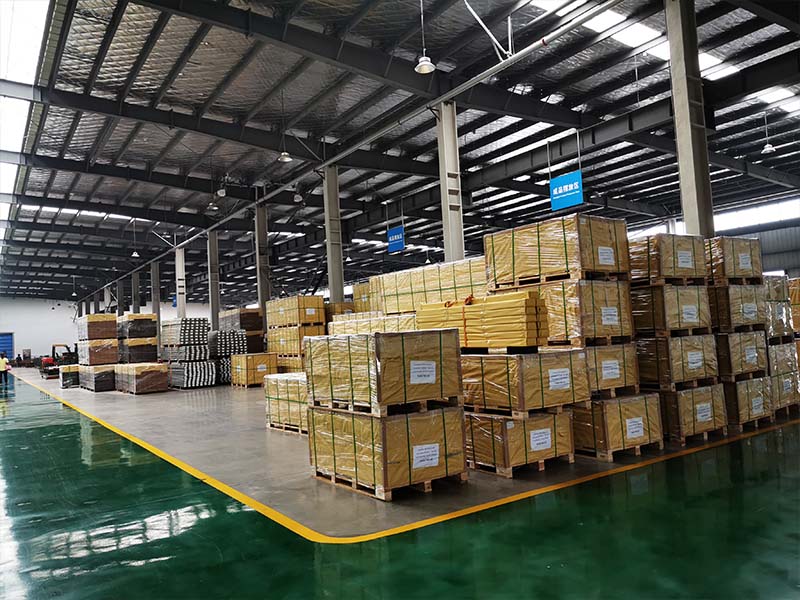
- Extrusion technology
At present, wood plastic processing and production are mainly divided into one-step method and two-step method.
PP/PE wood plastic is PP/PE recycled resin, fiber (wood fiber, bamboo fiber, rice bran, etc.); inorganic substances (calcium powder, talc powder); additives (lubricant, dispersant, compatibilizer, coupling (agent, toner, weathering agent, antifungal agent, etc.) are mixed in a high mixer to the required temperature, placed in a cold mixer, cooled to about 40-50 degrees, granulated by a flat twin granulator, and then added to the cone twin extruder The machine extrudes the product, which is a two-step production. The mixed material is directly added to the cone twin extruder to extrude the product without granulation, which is one-step production.
picture
One-step production process
picture - Selection of equipment and molds
- Mixing equipment
Traditional mixing equipment consists of hot mixing and cold mixing. Hot mixing is to add resin, fiber, inorganic substances, and additives into a hot mixing pot and use high-speed motion to heat up the additives to melt and disperse them in the resin and fiber inorganic substances. The more uniform the materials are dispersed, the more stable the production and product quality will be. The quality of material dispersion is related to its blade design and blade wear. The commonly used sizes of domestic hot mixing pots are 200L/300L/500L/800L. The cold mixing pot is where the hot-mixed materials are taken away by the low-speed operation of the motor and the circulation of water to reduce the temperature of the materials. The cold mixing of the materials to the temperature we set is beneficial to production and color stability, eliminating water vapor and reducing the decomposition of the materials. The sizes of cold mixing pots commonly used in China are 300L/600L/1000L/2000L
At present, many customers use ordinary mixers to mix raw materials according to the actual material conditions when the moisture content does not exceed 5%, and then directly put the materials into the granulator, and use the exhaust function of the granulator to remove excess moisture; when the moisture content is high In the case of 5%, use a hot mixer to mix the material, then directly enter the granulator, and use the preheating of the mixture for further granulation, which is also an energy-saving production method. - Selection of granulation equipment. There are two types of PP/PE wood plastic pellets: cone double and flat double. The effect of cone double PP/PE wood plastic pellets is not very good, mainly because the fibers are difficult to disperse and easy to agglomerate, which affects the use of the product. For example: the product has a high water absorption rate. Easy to get moldy, etc. Flat double granulation will not cause fiber agglomeration. Domestic PP/PE wood molding granulation basically adopts flat double granulation. The granulator produced by Dayun Plastic Recycling Auxiliary Equipment Manufacturing Co., Ltd., a subsidiary of Jwell, is directly crushed after granulation, and the material enters the extruder, saving time and energy.
- Selection of extruder: Domestic extruders basically use cone double to extrude products, whether it is a one-step method or a two-step method. Because the high content of PP/PE wood-plastic fibers causes serious wear and tear on equipment (screws and barrels), and in addition, fibers, additives, and PP/PE recycled materials will produce free acids after high temperatures, which will also cause certain corrosion to the screws and barrels. , so the quality of the screw barrel is very important. The dual-alloy screw barrel currently launched by the manufacturer adopts a segmented structure and full-alloy sintering technology for the inner hole, which can extend the service life of the screw barrel.
- Molds are the same as equipment. Good steel quality means good wear resistance and long service life. The quality of mold design is related to product quality, molding, product density, and production speed. In particular, solid thick products have higher requirements on molds.
- Selection of raw materials
- When choosing PP/PE recycled materials, it is best to choose recycled materials with a melting index that should not be too high, preferably below 1.0. The color should not be too dark, the particle size should be uniform, and the particles should be non-porous or have fewer pores. It is best to use first-grade recycled materials. Some recycled materials have been used several times and will reduce the mechanical properties.
- The fiber mesh number should be around 50-80, and fibers with low ash and moisture content are best (both ash and moisture are less than 5%) and the color should be consistent and uniform.
- Selection of additives. It is very important to make a good choice of PP/PE wood plastic additives. It is related to the stability and speed of production, the quality of the product (product molding, mechanical properties, mechanical properties, water absorption, and whether the product has additives during use. precipitation, etc.) and the service life of the product.
- Process selection
Domestic production of PP/PE wood plastic basically adopts a two-step process, which has the advantage of stable production and stable product quality. - Production process of raw materials:
Wood fiber is a highly water-absorbent material. Generally, the water content is about 15% or even higher, and the inorganic filler also reaches about 5%. The water content is a natural enemy that affects the production stability and product quality of plastics, especially wood-plastics, such as Affects the foaming ratio, water absorption of the product, deformation of the product, weather resistance and other physical properties of the product. Therefore, it is best to control the moisture content within 1%. Control the fiber and filler with reasonable moisture content—–add it to the high mixer—–mix it to 100 degrees—–add an appropriate amount of coupling agent—-mix it to 110-115 degrees– –Turn off the motor and open the mixer cover for 2-3 minutes —–Add PVC, stabilizer —–Mix to 80 degrees —–Add lubricant and other additives– —Add processing aids and foaming agent at 100 degrees——120-125 to unload the powder—–After the powder is unloaded, the motor stops, then open the big cover for 2-3 minutes and then mix the next hand material (It is best to mix five hand-made materials and clean the mixer once) —–The powder can be granulated or added to the twin-screw for production after cooling in the mixing barrel to 40 degrees (the mixing barrel must have circulating cooling water). When mixing ingredients, you must pay attention to the temperature and time. For example, it usually takes about 20-25 minutes to mix ingredients in a cold pot and about 12-15 minutes in a hot pot (the temperature is set to about 125 degrees). If the time difference is 3 minutes or more It may be that there is a problem with the temperature sensing line or the temperature control is inaccurate, or the horn knife of the mixer is seriously worn. This will affect the stability of the foaming ratio and color. When granulating, you should always pay attention to whether the temperature control temperature is accurate, whether the fan is operating normally, the size of the current, the particle size, surface, and length of the particles, whether the material is sticky, whether the feeding is stable, and there must be no interruption of the material. - Extrusion process: mainly pay attention to the following aspects
a. The key to setting the temperature of each section of the extruder is the compression section, metering section, and mold. The accuracy of each temperature control will affect the foaming rate and color. Foaming is mainly about setting the temperature of the compression section and metering section, and molding is mainly about the mold temperature. b. Normal operation of fans in each section.
c. The size and stability of the host current. If the host current fluctuates greatly, it means that the lubricant, processing aid, fiber and PVC components are not evenly dispersed.
d. The host speed must remain the same, because the speed will affect the foaming ratio and color.
e. The temperature of the dryer is generally set between 60-80 degrees, and is often kept at about 80% of the volume of the barrel. This is beneficial to production and color stability and improves the apparent quality of the product.
f. Different colors, different machines, length of storage time of rubber pellets, etc. have different temperature settings during production. In addition, wood-plastic foaming is greatly affected by the external environment and other factors, so the operator must know how to adjust the industry appropriately when different product abnormalities occur.