WPC Material: Wood-plastic composites (WPCs) have emerged as a game-changer in the construction and design industries, combining the best qualities of wood and plastic to create materials that are durable, versatile, and eco-friendly. These composites are made by blending wood fiber or flour with thermoplastics such as polyethylene (PE), polypropylene (PP), polyvinyl chloride (PVC), or polylactic acid (PLA). This unique combination not only enhances durability but also promotes sustainability by incorporating recycled materials into the mix. In addition to wood fibers and plastics, WPCs may also contain other lignocellulosic or inorganic fillers, broadening their applications across various industries.
Table of Contents
WPC Material: History of WPCs
The history of WPC technology dates back to the 1960s when Covema, a company based in Milan, Italy, pioneered the manufacturing process and patented it under the name Plastic-Wood. This breakthrough laid the groundwork for the widespread use of WPCs in numerous applications, including decking, fencing, and cladding. In the following years, other companies, such as Icma San Giorgio, contributed to the evolution of WPCs by patenting processes that enhanced their integration with thermoplastics. This innovation has led to WPCs becoming a staple material in construction, particularly in North America.
WPC Material: Diverse Applications
WPCs are incredibly versatile and have rapidly gained popularity in various applications. Initially dominating the outdoor decking market, they are now utilized for a wide range of purposes, including railings, landscape timbers, park benches, and interior furniture. WPCs provide excellent options for wpc wall panels, siding wpc, and exterior wpc wall panels.
HOSUNG, a leader in WPC manufacturing, offers a diverse selection of products designed to meet various needs. Their offerings include wpc decking, which is perfect for outdoor spaces, providing a natural wood look while being resistant to rot and decay. The wpc fence range provides durable options for securing property boundaries while enhancing aesthetic appeal.
Additionally, HOSUNG’s wpc fluted panels and 3D wpc wall panels offer innovative design solutions for interior and exterior applications, bringing both style and functionality. The hollow wpc products are designed to reduce weight without compromising strength, making them ideal for construction where every ounce matters. Furthermore, wpc ceiling panels add a touch of elegance to indoor spaces, while wpc gate panels ensure both security and beauty.
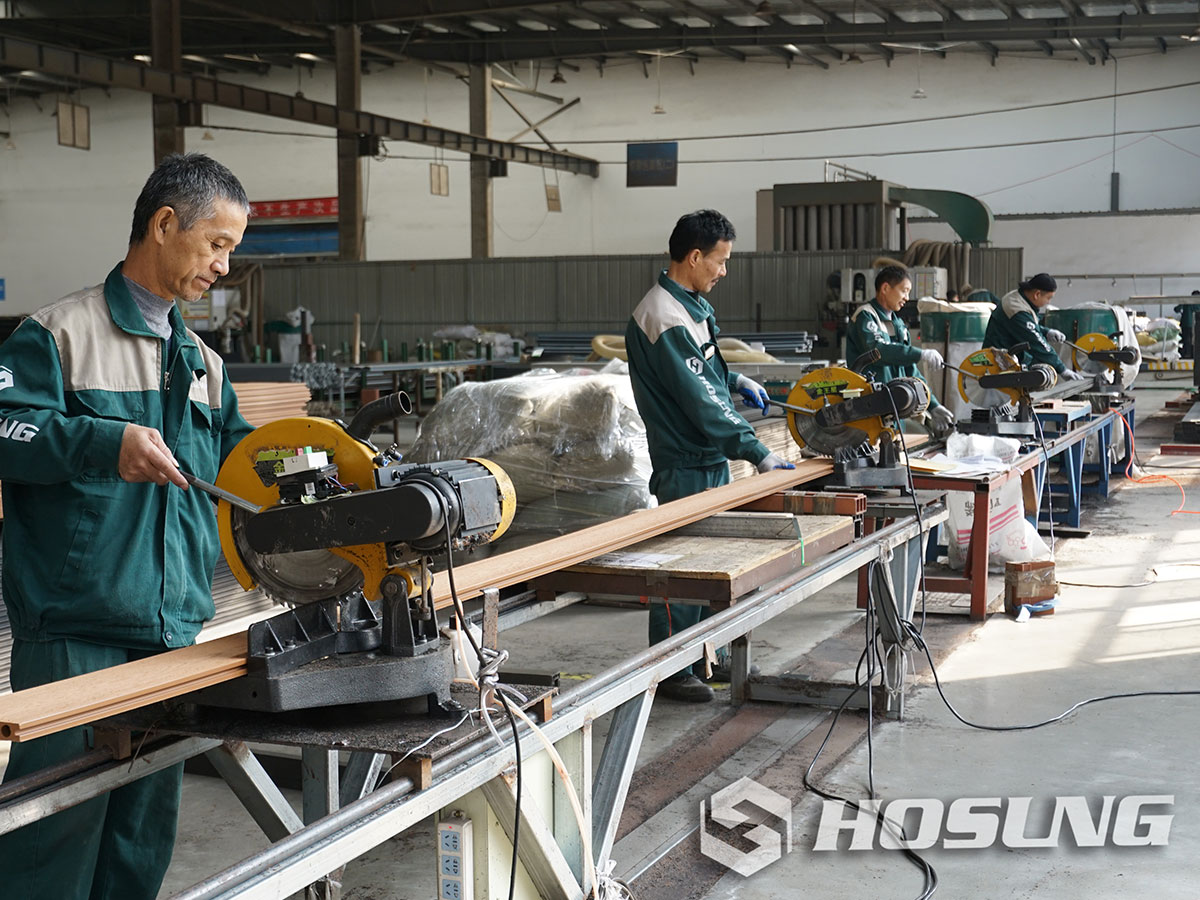
WPC Material: Production Processes
WPCs are produced by thoroughly mixing ground wood pellets with heated thermoplastic resins. The most common production method is extrusion, allowing manufacturers to create products in various shapes and sizes. Injection molding is also employed for specific applications. HOSUNG utilizes advanced production techniques to ensure that each wpc joist and wpc gate panel is crafted to the highest standards, combining quality with innovation.
Additives such as colorants, UV stabilizers, foaming agents, and lubricants are incorporated into the production process to enhance the performance and aesthetics of the final products. The versatility of WPCs allows for both solid and hollow profiles, providing a range of design options. The incorporation of organic materials means that WPCs can typically be processed at much lower temperatures than conventional plastics, reducing energy consumption during manufacturing.
WPC Material: Sustainability and Environmental Benefits
WPCs are often touted as a sustainable material due to their ability to incorporate recycled plastics and waste materials from the wood industry. This not only extends the useful life of discarded materials but also reduces the reliance on virgin resources. HOSUNG’s commitment to sustainability is evident in their production processes, which prioritize eco-friendly practices.
Despite their benefits, it’s important to note that WPCs have a considerable half-life of their own; the added polymers and binders can make recycling more challenging once the material reaches the end of its life cycle. However, they can be recycled into new WPC products, making them a viable option in sustainable building practices.
One major advantage of WPCs is their ability to be molded into virtually any desired shape, allowing for creative designs in various applications. WPC components can be bent and fixed to form strong, curved structures, opening up new possibilities for architects and builders. Additionally, WPCs do not require painting, which reduces maintenance efforts. They are available in a variety of colors, with gray and earth tones being particularly popular.
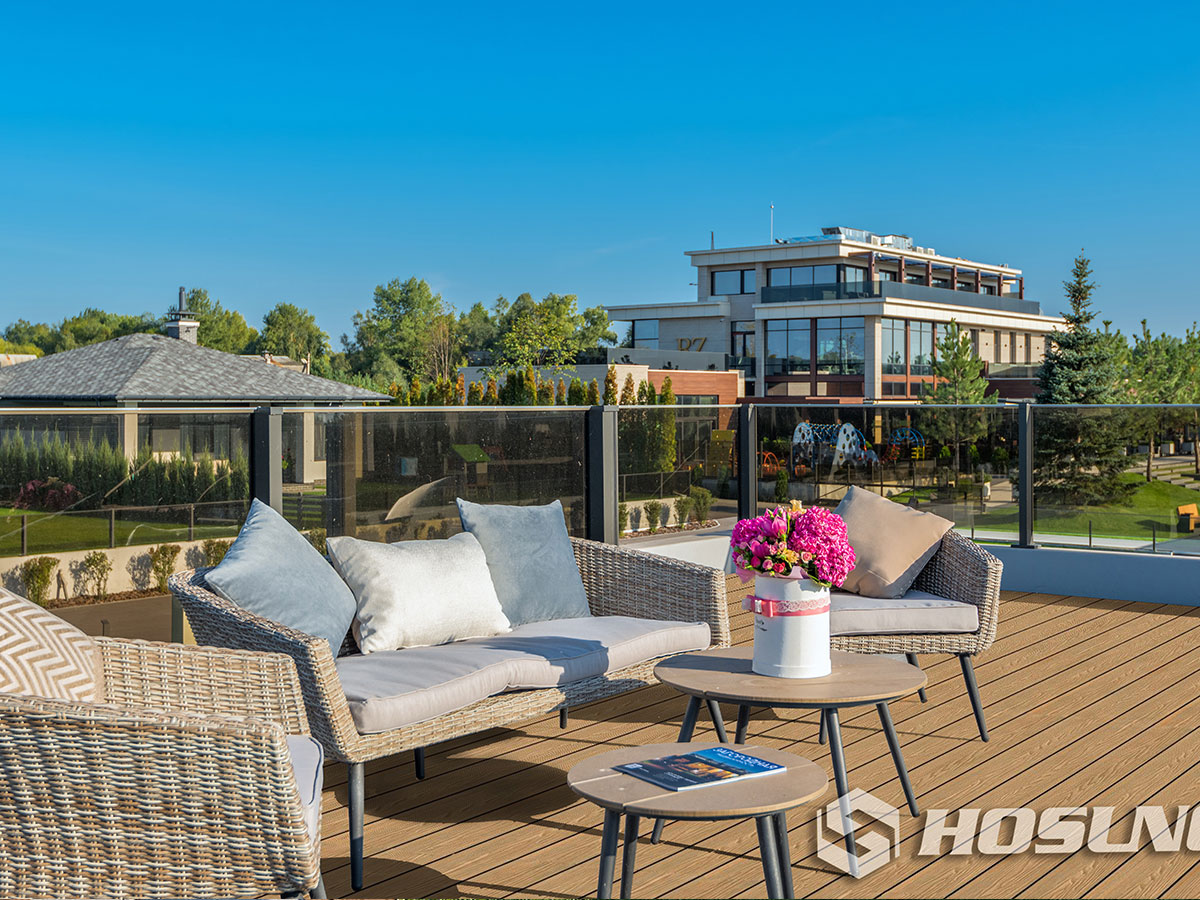
WPC Material: Performance Characteristics
Despite having a cellulose content of up to 70% (though a 50/50 ratio is more common), the mechanical properties of WPCs are most similar to those of pure polymers. This means that WPCs typically exhibit lower strength and stiffness than solid wood, and their behavior can be affected by factors such as time and temperature.
Wood particles in WPCs can be susceptible to fungal attacks, though this vulnerability is less pronounced than in solid wood. Meanwhile, the polymer components may degrade when exposed to UV light, necessitating consideration of material selection based on environmental conditions. Freeze-thaw cycles may also impact strength and stiffness, though ongoing testing aims to address these challenges.
In summary, wood-plastic composites represent a significant advancement in building materials, offering a combination of durability, aesthetic appeal, and low maintenance. HOSUNG’s extensive range of products—including wpc decking, wpc fencing, wpc cladding, and more—ensures that customers can find the perfect solution for their construction needs. Whether enhancing outdoor areas with wpc wall panels or creating striking interiors with 3D embossed panels, HOSUNG provides innovative, high-quality options that meet modern sustainability demands. With the growing interest in WPCs, their applications will continue to expand, making them a vital component of the future of construction and design.